|
Page 2 of 2 |
Author |
Message |
Warpspeed Guru
 Joined: 09/08/2007 Location: AustraliaPosts: 4406 |
Posted: 01:20am 25 Apr 2017 |
Copy link to clipboard |
 Print this post |
|
If I was starting out from zero,with a clean sheet of paper design, and I wanted to keep it fairly simple (no microprocessor, no software). I would use a boost converter, not a buck regulator.
That would step UP the voltage to any required level, and you have complete control over the loading of the turbine blades at every wind speed. Cut in speed would be essentially zero, although you would probably be getting milliwatts with the blades barely moving.
Starting out with this concept in its most primitive form, we would first rectify our wind turbine to get some useful dc at a voltage lower than the final battery voltage. We feed that into a boost converter which consists of a series dc choke, mosfet down to ground, and a series diode.
We can then PWM the mosfet so it turns on for some short duty cycle. The current builds up in the choke, and when we turn off the mosfet there will be a huge back EMF generated by the choke which dumps a packet of charge into the battery, regardless of battery voltage.
By adjusting the duty cycle we can vary the loading on the wind turbine to move our power peak over a very wide range of input voltages and input power, and our battery voltage does not really matter, as long as its always higher than the voltage coming out of the wind turbine.
That is the bare bones of it. Obviously you need to adjust the potentiometer every time the wind speed changes to relocate the duty cycle at the new peak power point.
So what we do is hook up an anemometer to give us a voltage that has some relationship to wind speed. Measure that with an analog to digital converter, and (for simplicity) we determine which of four wind speed ranges we are currently in.
We then have either four LEDs or a digital display that reads 1-4.
Associated with that might be four potentiometers that we can tweak for max battery charging current in each wind speed zone. If we are wind speed range three we tweak potentiometer three for maximum charging current just short of blade stall.
Of course you can have as many potentiometers as you wish. And you could get a very nice smooth curve, and make it any shape you want. And it will change up and down in turbine loading and MPPT track almost instantly without any instability problems.
The software geeks would say put it ALL into an Arduino, and that would be very sensible thing to do.
But you could just wire up a few very basic chips and some potentiometers on a breadboard, and it should work just as well initially to experiment with initially.
I am having trouble posting a diagram, will come back to that.
Cheers, Tony. |
|
Warpspeed Guru
 Joined: 09/08/2007 Location: AustraliaPosts: 4406 |
Posted: 01:23am 25 Apr 2017 |
Copy link to clipboard |
 Print this post |
|
 Cheers, Tony. |
|
DaveP68
 Senior Member
 Joined: 25/11/2014 Location: New ZealandPosts: 292 |
Posted: 03:11pm 25 Apr 2017 |
Copy link to clipboard |
 Print this post |
|
Hi Tony
Well you could be onto a winning concept here to improve the power output curve as illustrated for these F&P stators.
It just so happens the 6x 2p Delta wired 36 pole copper stator is just the unit to try with the above set up. Peak voltage should be about 28 close to what you have in the concept drawing.
Taking into account a the float voltage of a 48 V battery system is around 56 VDC then the up to 50 % duty cycle on the PWM control is within limits.
At just over 500 RPM it should output 28 VDC at 18 Amps ~ 500 W. It may even do 550-600 W. If the capacitor after the 3 phase rectifier is sized correctly the PWM pulses will draw the peak current from the stator with out the voltage dropping of at the same proportion.
Did a test on a lathe a few months back with a PWM dynamic brake circuit and got 1830 W @ 1155 RPM. Dynamic brake was set to cut in at 455 VDC and current was 4.02 Amps. That's was using a 36 pole copper stator wired as just Delta with a black rotor cap. That's 1.59 W per RPM. These stators do put a bit more power out above 700 RPM so below that ratio may be a bit lower.
Here's a photo of the same dynamic brake being used to extract around 1 kW at 908 RPM.
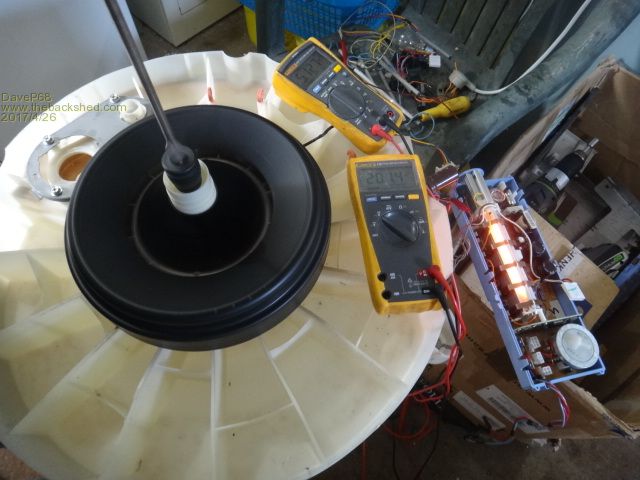 Note the orange glow of the resistor in the top of the blue cased module.
Cheers
DavidEdited by DaveP68 2017-04-27 There are realities if you do not accept, will lead to frustration because you will be spending time on wrong assumptions and the results cannot follow! The Dunning Kruger Effect :) |
|
Warpspeed Guru
 Joined: 09/08/2007 Location: AustraliaPosts: 4406 |
Posted: 04:44pm 25 Apr 2017 |
Copy link to clipboard |
 Print this post |
|
Its not quite the same driving one of these alternators with a drill motor or a lathe, as driving it with a wind turbine. With a motor you can keep loading the output and getting more and more power out, right up until something smokes.
With a wind turbine, the blades are going to stall at some point, and the load needs to be backed off a bit from that.
Anyhow, your figures of 28v and 18 amps input are a good starting point for a boost converter. The heart of that will be the energy storage choke.
Being a frugal sort of chap, and always looking to use up junk I already have, and that other Forum members may also have lurking somewhere, one of those funny chokes fitted to many grid tie inverters would probably be a good candidate.
These are typically 2.5mH to 3mH and examples I have tested saturate at 30 amps or more.

For testing we really need a real wind turbine and a real battery, and I know you have not quite reached that stage yet. Cheers, Tony. |
|
DaveP68
 Senior Member
 Joined: 25/11/2014 Location: New ZealandPosts: 292 |
Posted: 11:21pm 25 Apr 2017 |
Copy link to clipboard |
 Print this post |
|
What I was trying to point out, is peak power with no reference to cut in RPM, or what the low to medium wind speed power extraction will be. That is the job of the PWM controller to manage the duty cycle from basically zero to up to that 50 %.
This is why I gave some examples of what these stators can do at high RPM on a lathe & drill. With a set of 3 m wind turbine blades spinning at around 500 RPM in 40 kph winds there could be 2.3 to 2.5 kW of shaft power to turn a PMA(s).
Up to and close to 50% duty cycle is going to be the trick part to design, but easier to manage when it comes to things not blowing up.
By my calculations a cut in of 100 RPM will provide 10 VDC, with limited current due to lack of shaft power in low wind speed of say 3 m/s.
I'm a frugal type too The only expense incurred in the last 18 months testing different stators is $99 for that 1200 W drill & $48 for some 35 Amp 400 VDC rectifiers. All the other hardware including the stators/rotor caps came free from scrapped machines I couldn't repair. Got at least 5 of each stator type in the workshop. Also have over a 100 of 270 uf 250 VDC capacitors from the F&P motor control boards used to make capacitor doubler circuits.
Need to get some chokes to play with too. As got over a 100 IRF840 MOSFET's which I could put to future use on a high input voltage range inverter project.
Don't need a battery as my dynamic brake circuit can be set to any voltage 40 to 460 VDC. Currently it's current limited, but an up grade is happening soon as want to give it the capability of 30 + Amps in the 40 to 60 V range. Have lots of 20 & 28 ohm high power resistors each rated at 300 W. These can be in a mixture of series or parallel configurations to make loads from 1 ohm to say 300+ ohms to simulate a battery or inverter input.
So all that is left is get an actual wind turbine up and flying.
In the interim I'm helping out Fred flc1 who is in the process of rebuilding his wind turbine with some of Phill's GOE 222 blades. That's why I went to all the effort to re wire that 6x 2p 36 pole copper stator for him. It took 5 hours! Also supplying him with a set of capacitor doublers to try out at no charge as all the parts came for free at my end.
Cheers
David There are realities if you do not accept, will lead to frustration because you will be spending time on wrong assumptions and the results cannot follow! The Dunning Kruger Effect :) |
|
Warpspeed Guru
 Joined: 09/08/2007 Location: AustraliaPosts: 4406 |
Posted: 02:54am 26 Apr 2017 |
Copy link to clipboard |
 Print this post |
|
[quote]By my calculations a cut in of 100 RPM will provide 10 VDC, with limited current due to lack of shaft power in low wind speed of say 3 m/s.[/quote]
The point with a boost converter, it will still supply power at any reasonable output voltage even if the input voltage was below one volt, or even less. Power will obviously be negligible under those conditions. But it will still be doing something. So really with a boost converter there will be no longer be anything that behaves like a particular cut in speed.
The cubed law thing will go right down to zero provided the PWM control electronics and drive to the mosfet gate can be sustained.
I once built a very small boost converter to power a Geiger counter tube that generated +450 volts dc from a pair of 1.5 volt AA batteries. Same circuit, choke, mosfet and diode, driven by a cmos 555 timer. Cheers, Tony. |
|
DaveP68
 Senior Member
 Joined: 25/11/2014 Location: New ZealandPosts: 292 |
Posted: 10:10pm 26 Apr 2017 |
Copy link to clipboard |
 Print this post |
|
I do understand that factor. All I'm trying to point out is there is a minimum RPM that any power can be extracted from the blades without creating a stalled condition. I'm sure you understand all these other factors too.
It takes about 6-7 W of shaft power "per F&P stator" just to get them turning, which is still energy that must be extracted from the wind. Measured form monitoring the power consumption of a cordless drill in direct drive mode and subtracting it's minimum drive power to turn it self.
So what this means is there will still be a form of cut in RPM for the blades to start turning. Once tuning they will still run at a slightly lower wind speed. With the 6x 2p Delta stator that could be as low at 40 to 50 RPM.
They way I see it, is the PWM control system will be self powered from a minimum current draw from start up once the blades start turning. If that happens to be 4-5 VDC that is more than enough to work with.
On the subject of your Geiger counters, how well did it work? Were you able to get it calibrated to show a meaningful reading?
Sounds like you've a variety of different projects on the go.
Cheers
David There are realities if you do not accept, will lead to frustration because you will be spending time on wrong assumptions and the results cannot follow! The Dunning Kruger Effect :) |
|
Warpspeed Guru
 Joined: 09/08/2007 Location: AustraliaPosts: 4406 |
Posted: 10:51pm 26 Apr 2017 |
Copy link to clipboard |
 Print this post |
|
Point taken. A boost converter is probably still the most efficient method of extracting power under extremely marginal wind conditions.
The Geiger counter works fine, I have been monitoring the background radiation here in Melbourne since shortly after Fukushima.
Each tube has a calibration factor proportional to its size and geometry. Every time an energetic ionising photon passes through the tube, it momentarily breaks down for a few microseconds, and that is one count. Physically larger tubes record higher counts for the same background level.
If you know that your tube collects 22 counts per minute at 0.1 microsieverts per hour, to display ".100" it would take 4.545 minutes to count up to 100.
So all you need is a digital counter that counts up over that exact known period, and it will then read directly in microsieverts per hour, updating about each four and a half minutes. It could just as easily read in other units if the measurement period is adjusted accordingly. Current readings in Melbourne jump around all over the place between about 0.065 and peaking at 0.1 microsieverts per hour. In Japan I believe its between about 3.0 and 1.5 with 0.5 being considered very low over there.
Yes, far too many projects to think about. Cheers, Tony. |
|
DaveP68
 Senior Member
 Joined: 25/11/2014 Location: New ZealandPosts: 292 |
Posted: 03:53pm 28 Apr 2017 |
Copy link to clipboard |
 Print this post |
|
Have been to the Hiroshima Peace Memorial Museum. As part of an exhibit there's a Geiger counter with small piece of radioactive material set up on a short rail. It can be moved close to the detector or up to 1/2 a meter a away.
The interesting part was watching the decay of the reading at a logarithmic rate (square law) as the radioactive source was moved away from the detector.
Your observation of background radiation is some what different to what I played with in the museum, in that the source is very low but always there. With out being able to remember the readings as it was a long time ago, I could walk away from this source even though it would have been low anyway.
Will have build my own Geiger counter to check the local back ground radiation where I reside here in central Auckland. I'll be able to learn a bit about small boost converters in doing so.
Cheers
David There are realities if you do not accept, will lead to frustration because you will be spending time on wrong assumptions and the results cannot follow! The Dunning Kruger Effect :) |
|
Warpspeed Guru
 Joined: 09/08/2007 Location: AustraliaPosts: 4406 |
Posted: 04:21pm 28 Apr 2017 |
Copy link to clipboard |
 Print this post |
|
Plenty of low cost Russian surplus Geiger tubes that are long term regulars on e-bay. The Ruskies must have made millions of them during the cold war.
There are a number of very different sensitivity ranges depending on what you want to use the tube for. The really physically small (very low cost) tubes look like a 5AG glass fuse, are only really useful for locating very high levels of radiation, looking for leaks in reactor pipework, measuring potentially lethal doses after a nuclear attack, and that type of thing. These are pretty hopeless for measuring general low background levels. You might see about one count every ten minutes if you are lucky.
A good useful mid range sensitivity tube is the SB20, which is what I have. This is a very popular tube for home projects, with plenty of information about it available on the internet. Should get you about 10 to 30 counts per minute.
The pancake detectors are supposed to be even more sensitive, ideal for measuring radiation levels in food samples for example, where you don't want to wait several minutes to accumulate sufficient counts to be useful. I have a pancake detector here, but have never tried to use it.
All jolly good fun and very instructive.Edited by Warpspeed 2017-04-30 Cheers, Tony. |
|
|
Page 2 of 2 |