|
Page 2 of 2 |
Author |
Message |
martinjsto
 Senior Member
 Joined: 09/10/2007 Location: AustraliaPosts: 149 |
Posted: 06:55am 31 Oct 2007 |
Copy link to clipboard |
 Print this post |
|
wait a minute,
its working
i realised the pot wasnot working propely i changed it and now seems ok
thanks a million gill
martin free power for all
McAlinden WA |
|
GWatPE
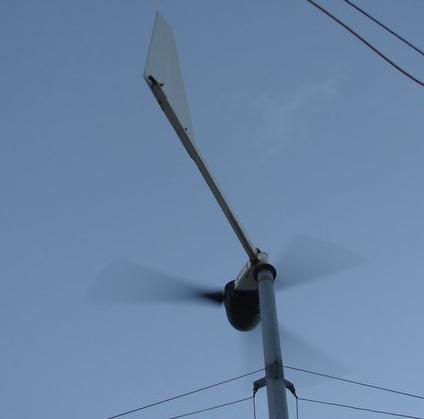 Senior Member
 Joined: 01/09/2006 Location: AustraliaPosts: 2127 |
Posted: 08:11am 31 Oct 2007 |
Copy link to clipboard |
 Print this post |
|
Hi Gill and martinjsto,
I have just been reading this thread and the oatley design uses some hysterysis built into IC2A with R6 and C3. This schmidt trigger has built in input hysterysis at 2/3 VCC and at 1/3 VCC.
Any loads running directly from a battery like incandescent lights will display the minute changes as battery voltage is regulated by the shunt. This is a property of the filament converting current to light.
I now have a picaxe shunt regulator design that has programmable hysterysis and delay times. It should be possible to use the PWM output to throttle the dump load proportional to the excess power.
The code would be similar to the MPPT on the other thread. I will look into it if readers think it may be of use.
cheers, Gordon.
become more energy aware |
|
RossW Guru
 Joined: 25/02/2006 Location: AustraliaPosts: 495 |
Posted: 08:50am 31 Oct 2007 |
Copy link to clipboard |
 Print this post |
|
Martin: I'm keeping a low profile for a while, but if you continue to have issues with my "junkbox bits" controller, please private message me, or come bug me on irc.albury.net in #aussiere
The design is "simplistic" - sure, it has some shortcommings, but it's simple, has hysteresis, time delay and adjustable setpoint. Quite a few have built it and had good results with it.
The FET should be just about any suitable amperage n-channel mosfet you can get. Because its driven directly from the opamp output, either logic level fets, or more conventional ones needing 10V on the gate should all work reasonably well. I have (intentionally) designed it to work with a variety of components (almost any opamp will work, almost any fet will work, you can fiddle the resistor values and cap values to suit what you have on hand etc)
Cheers,
R. |
|
Gill
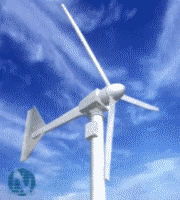 Senior Member
 Joined: 11/11/2006 Location: AustraliaPosts: 669 |
Posted: 10:57am 31 Oct 2007 |
Copy link to clipboard |
 Print this post |
|
There you go Martin, Ross is 'The Man' if you have anymore problems getting your regulator purring. He may even help fault find the K220 too. A working backup is a good idea and it's bound to be just one component causing the trouble with it also.
Gordon,
I was my dream to have the Gizmo Data Logger with it's LCD readout but with a PWM regulator instead of the existing one. I felt his design lent itself to modification to PWM. I have bought the display and PICAXE28x and that expensive little current sensing thingie(I know the cheaper way is now suggested) but a new mill has got in the way so never got to attempt the PWM modification. I think this would still work hand in hand with your project but for MPPT controller best incorporated into it??????? was working fine... til the smoke got out.
Cheers Gill _Cairns, FNQ |
|
martinjsto
 Senior Member
 Joined: 09/10/2007 Location: AustraliaPosts: 149 |
Posted: 03:14pm 31 Oct 2007 |
Copy link to clipboard |
 Print this post |
|
thanks to you all, its working well now
im now trying to design a circuit board for this schematic using pad2pad.
thanks ross for your design my main prob was the orientation of the fet and a faulty 20k variable resistor. all seems good now, i will callibrate tomorow.
i will be sure to credit you on the board once i have made one. I get a lot of emails from people who would like a reasonable controler for there setup (i have been selling wind chargers on ebay) do you mind if i was to make these and onsell to people who want them. I dont want to "tread on your toes" or steal your design by no way, i only charge for time and component costs.
my email is martinjs@iinet.net.au pls let me know your thoughts.
thanks again
martin free power for all
McAlinden WA |
|
GWatPE
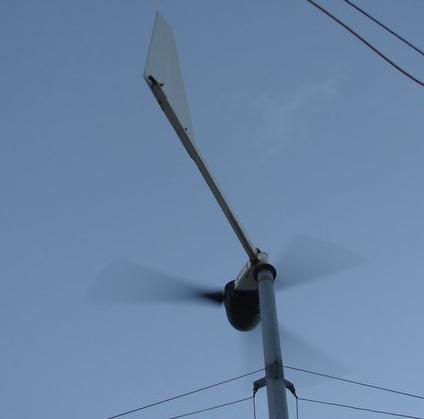 Senior Member
 Joined: 01/09/2006 Location: AustraliaPosts: 2127 |
Posted: 10:55pm 31 Oct 2007 |
Copy link to clipboard |
 Print this post |
|
Hi all,
Sorry Ross,
I now have code for a PWM regulator.
This is for you Gill,
The picaxe has a minimum frequency PWM of 4kHz. This will probably mean any dump load will make some noise.
This cct will regulate the battery voltage at any programmed level. On a 24V system I operate my regulator at 29.5V.
I will have to test the code on a prototype as at 4kHz the PWM output variable has a word variable type instead of a byte.
the code is posted here
' system loads when battery voltage exceeds 29.5V
' pin 6, ADC1 battery sense voltage
' pin 3, ADC4 unused
' pin 5, PWM2 is mosfet drive output
' pin 7, OUT0 unused
' pin 4, IN3 unused
Symbol BatVolts = W1
Symbol PulseWidth = W0
Start:
pwmout 2, 249, 0
PulseWidth = 0 'Set a min range pulsewidth when control starts
Main:
readadc10 1, BatVolts 'Read a battery voltage value
if BatVolts = 500 then steady 'system steady, leave alone
if BatVolts < 500 then Down 'UnLoad battery a bit more
if BatVolts > 500 then Up 'load battery a bit more
Up:
if pulsewidth > 999 then mmax
PulseWidth = PulseWidth + 1
pwmout 2, 249, PulseWidth
goto Main
Down:
if pulsewidth = 0 then mmin
PulseWidth = PulseWidth - 1
pwmout 2, 249, PulseWidth
Goto Main
steady:
pwmout 2 , 249, PulseWidth
goto Main
mmax:
pulsewidth = 1000
pwmout 2, 249, PulseWidth
goto main
mmin:
pulsewidth = 0
pwmout 2, 249, PulseWidth
goto main
This will increase pulse width when voltage is above set point and decrease pulse width when voltage is below. The picaxe has about a 3 second response time from PWM fully OFF to fully ON.
The mosfet will probably require a small heatsink as there will be some heating from switching loss.
This cct will proportionally load the mill to maintain the battery voltage. There will be no sudden ON/OFF.
PS. I am all for good simple ccts, but the micro is a single chip solution to many control tasks. I have also tried the NHP Alpha [photo posted obove]. I only use it for an LCD to display system voltage and power readings now.
cheers, Gordon.
become more energy aware |
|
GWatPE
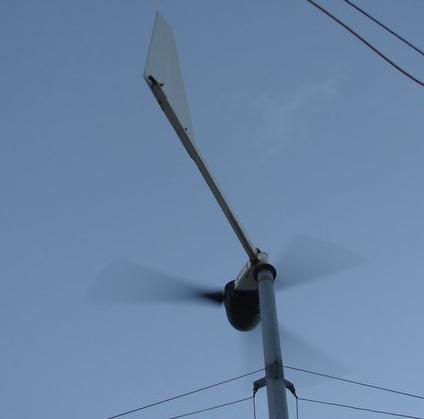 Senior Member
 Joined: 01/09/2006 Location: AustraliaPosts: 2127 |
Posted: 03:12am 01 Nov 2007 |
Copy link to clipboard |
 Print this post |
|
My mistake, the RC combination in the oatley cct is R7 and C3. This is the timing OFF delay. The on delay is R6-C3, much shorter. The voltage hysterysis is provided by the schmidt trigger action in the comparator of IC1. I hope this clears this up.
I have tested the PWM using the picaxe. The cct reponds fast enough to use as a mill dump regulator. On test a 5 second response from fully OFF to fully ON. The best part of the PWM is that the dump load can be much higher power rating than the mill and the system still works.
With a constant mill output, the cct will find the optimum PWidth to maintain the battery voltage.
I used a simple resistor divider as the sensor.
This would be ideal for interested readers wishing to try a cheap-cheap regulator software solution.
This is not as severe on the mill or battery as ON/OFF control.
I will add this improved cct to my mill now.
cheers, Gordon. become more energy aware |
|
Highlander
 Senior Member
 Joined: 03/10/2006 Location: AustraliaPosts: 266 |
Posted: 06:25am 01 Nov 2007 |
Copy link to clipboard |
 Print this post |
|
G'day GWatPE, bloody hell a cheap pwm shunt reg.
You could give oatley a run for their money.
Why don't you do a kit and put them on ebay?
The oatley ones are even sold in the states, and they are bang,bang type @ around $50 au.
Might be a good little sideline. Central Victorian highlands |
|
GWatPE
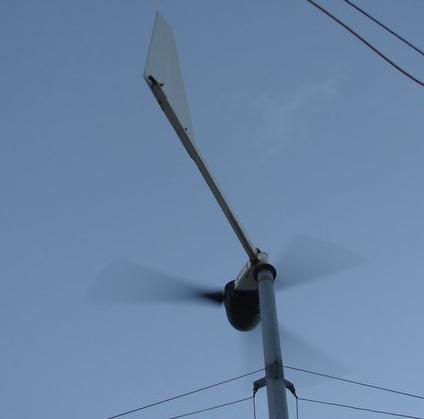 Senior Member
 Joined: 01/09/2006 Location: AustraliaPosts: 2127 |
Posted: 07:18am 01 Nov 2007 |
Copy link to clipboard |
 Print this post |
|
Hi highlander,
yeh, cheap-cheap.
The mosfet driver would be the most expensive part. I could take orders, maybe!
I only design, build with SMD these days.
I avoid drilling holes. I only use screened PCB.
If enough readers were interested, a limited run might be worthwhile.
I am not sure if many novices could handle soldering 1/4 size IC's with 0.025" pad spacing. Not the sort of PCB you can CNC make. I think the smallest carbide router is 1mm. I use ferric chloride and photo reduced artwork.
You would have seen some of my proto- boards on other posts. My local office supply makes the reductions for 75c.
My favourite FET is a 60V160A TO-220.
I will wait for some more feedback.
cheers, Gordon.
become more energy aware |
|
Gill
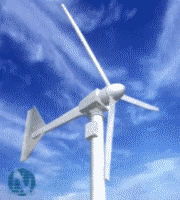 Senior Member
 Joined: 11/11/2006 Location: AustraliaPosts: 669 |
Posted: 11:04am 01 Nov 2007 |
Copy link to clipboard |
 Print this post |
|
Gordon,
Simple & cheap PWM reg.
Your description sounds great and the code is simple enough that even I can follow it.
Excellent! Thank you.
I'm guessing that adjusting the set point voltage is done by a trim pot in the voltage divider?
I think most would want a schematic to build it though.
And there'd be a few who'd prefer to buy one assembled.
Any idea of ball park $ ?
was working fine... til the smoke got out.
Cheers Gill _Cairns, FNQ |
|
martinjsto
 Senior Member
 Joined: 09/10/2007 Location: AustraliaPosts: 149 |
Posted: 12:07pm 01 Nov 2007 |
Copy link to clipboard |
 Print this post |
|
hi guys, great idear on the pmw regulator gordon , sounds like a smart charger.
i would be interested in purchasing a complete pmw regulator assembly also, as i could not solder such a small ic circuit
when you have worked out the details, let us know how much for a unit.
thanks
martin free power for all
McAlinden WA |
|
GWatPE
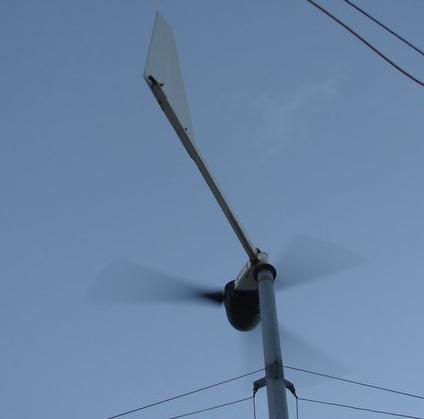 Senior Member
 Joined: 01/09/2006 Location: AustraliaPosts: 2127 |
Posted: 11:00pm 01 Nov 2007 |
Copy link to clipboard |
 Print this post |
|
Hi all,
Gizmo wrote
I would try a 10k pot with 22k series resistor between pins 2 and 7 of the L4949. The will provide some feedback, you may have to play around with the values a bit.
This would add negative feedback. I cannot see how this helps hysterysis.
It would have been better to connect a high value resistor between pin 3 or 4 of IC2 to give some positive feedback. RossW has the right idea in his junk box cct. The 470k feedback resistor is for positive feedback.
Hi Gill,
I would not normally ues a pot, but provision could be made. A default setting could be 24V, but the code could be made auto detect on power up for 12,24,36V. probably no additional componentry.
The regulator is not a precise tool. You have to admit that what will be replaced is pretty crude.
I would use a 29.5V setting for 24V battery. The battery life would not be seriously shortened unless the system was heavily over powered.
I will cost out a cct if enough people are interested.
Hi Martinjsto,
I think the mill is the charger, the PWM only regulates the voltage on the battery.
I will be hooking the proto cct up to my mill soon. I will use a 1.5 ohm 300W dump resistor. A good use for some audio dummy load resistors.
cheers, Gordon. become more energy aware |
|
GWatPE
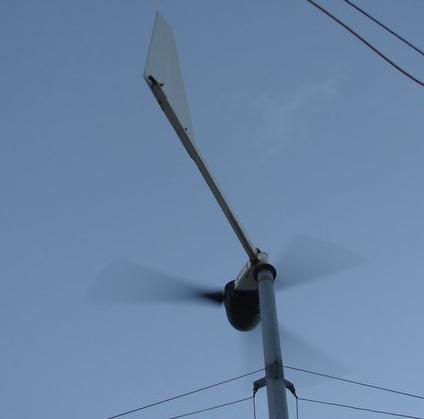 Senior Member
 Joined: 01/09/2006 Location: AustraliaPosts: 2127 |
Posted: 03:39am 02 Nov 2007 |
Copy link to clipboard |
 Print this post |
|
I will create a new thread related to PWM regulator.
cheers, Gordon. become more energy aware |
|
commanda Newbie
 Joined: 12/11/2007 Location: AustraliaPosts: 14 |
Posted: 08:44am 18 Nov 2007 |
Copy link to clipboard |
 Print this post |
|
You can also employ an LM3914 bar graph led display driver to make a step controller.
I went totally overboard with mine. I latched the outputs and clocked it at 30 seconds. I used XOR gates on all the output fets to fault detect (open cct load, open cct or short cct fet, blown fuse). Fault cct has a sonalert and mute switch and led which flashes while muted. It also has an equalise/boost mode which is manually started, and self times out. And a battery temperature meter which will also cancel boost mode. And the boost mode timer operates in accumulate mode. If the wind stops blowing, the timer halts counting until the charge current picks up again. And the very last step on the LM3914 also triggers the alarm.
It is, however, considerably more complex to build than anything discussed here.
Amanda |
|
GWatPE
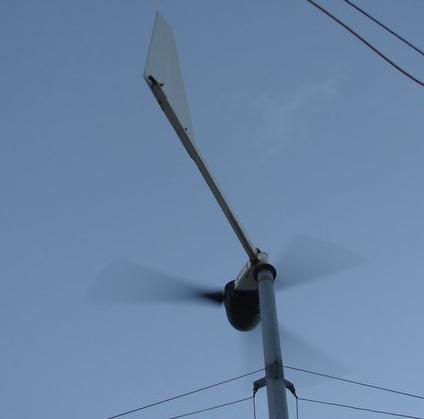 Senior Member
 Joined: 01/09/2006 Location: AustraliaPosts: 2127 |
Posted: 06:55am 19 Nov 2007 |
Copy link to clipboard |
 Print this post |
|
Hi Amanda,
I have used an LM3914 as a step controller for an airconditioning plant in 1976. There are limitations with this chip, notably the tendency for overlap with outputs. I see you latched the outputs. I thought the outputs were current limited open collector.
I am tending to design excusively now with the PIC chips. I have simplified my design layouts and they are much more flexible. I have reduced cct component count by at least a factor of 2. The complexity is put into some code.
I am waiting in earnest for the picaxe 28X2.
cheers, Gordon.
become more energy aware |
|
commanda Newbie
 Joined: 12/11/2007 Location: AustraliaPosts: 14 |
Posted: 08:08am 19 Nov 2007 |
Copy link to clipboard |
 Print this post |
|
Part of my goal is long-term maintainability (is that a word?) well into my old age and senility. Anything micro and programmable doesn't fit with my paradigm.
If you put the base-emitter junction of a pnp transistor in series with each led of the LM3914, you now have a switched voltage output. In my case I feed this into a 74HC374. The '374 is then clocked, and the outputs drive the fet gates.
The LM3914 is run in bar mode (not dot mode) so the overlapping outputs is not a problem.
Amanda |
|
GWatPE
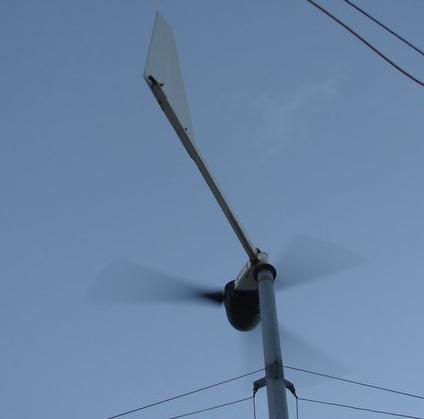 Senior Member
 Joined: 01/09/2006 Location: AustraliaPosts: 2127 |
Posted: 11:01pm 19 Nov 2007 |
Copy link to clipboard |
 Print this post |
|
Hi Amanda,
I don't see why you are worried with micro designs. A computer has a clock, runs a program, has some inputs and has some outputs. I think that the dump controller you posted on another thread has these features. Is D14 used to indicate if the fuse has failed?
Discrete component designs will still have a place, even in my designs.
I hope some of the readers can benefit from your postings.
cheers, Gordon.
become more energy aware |
|
|
Page 2 of 2 |