|
Page 1 of 2 |
Author |
Message |
aorn318
 Newbie
 Joined: 05/09/2010 Location: AustraliaPosts: 20 |
Posted: 10:39am 18 Sep 2010 |
Copy link to clipboard |
 Print this post |
|
Hi guys have had heaps of fun with my F/P test unit earlier in a post i commented on making a multiple stator on a single shaft gear driven. since then with an amount of thinking I have moved to axial flux approx 24inch coil plate solid mounted (big i know but as they say bigger is better) shaft driven using 2 BMW drive units to transfer the power to ground level
Has anyone tried this or can anyone give an insight as to the power loss from the prop to the gen
I want to have the generator in the power room at ground level this i hope would make the whole system easier to mount on the tower
as its still only early days i only have a sketch of the idea but as i get things together i will post with pics If it ain't broke don't fix it |
|
Downwind
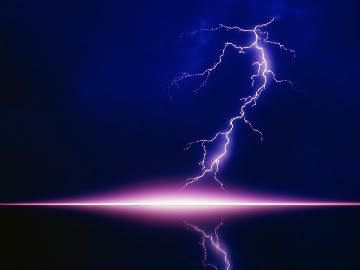 Guru
 Joined: 09/09/2009 Location: AustraliaPosts: 2333 |
Posted: 11:00am 18 Sep 2010 |
Copy link to clipboard |
 Print this post |
|
Basically every transfere of power you loose.
So for every gear drive you loose energy meaning what the prop puts in you will get less out then you will with straight shaft from prop to alt.
There is so much chatter on the forum about friction loss in bearings lead alone losses in drives.
Folkes remove the seals from bearings to reduce losses and you want to use right angle drives??
I think you are heading in the wrong direction.
Pete. Sometimes it just works |
|
aorn318
 Newbie
 Joined: 05/09/2010 Location: AustraliaPosts: 20 |
Posted: 11:45am 18 Sep 2010 |
Copy link to clipboard |
 Print this post |
|
even so there is always going to be % loss you just need a generator capable of dealing with the loss i think im going to toy with the idea or to put it differently flog a dead horse but as long as the F/P keeps the power coming then it cant hurt to go out on a limb If it ain't broke don't fix it |
|
VK4AYQ Guru
 Joined: 02/12/2009 Location: AustraliaPosts: 2539 |
Posted: 01:49pm 18 Sep 2010 |
Copy link to clipboard |
 Print this post |
|
Hi Aorn318
I used a differential to transfer power in a VAWT it was a step up drive running in the crown wheel and out the pinion it was a bit lossy but not as bad as v belts I also tried, I used ATF in the diff to cut oil drag but still lost about 10% so with two it would be a bit lossy. I reduced the preload on the bearings to nearly zero that helped but still suffered losses.
I checked on a tractor PTO right angle drive specs and they say 15% loss, but that,s with tight bearings and EP 140 oil so that could be reduced.
All the best
Bob Foolin Around |
|
aorn318
 Newbie
 Joined: 05/09/2010 Location: AustraliaPosts: 20 |
Posted: 10:16pm 19 Sep 2010 |
Copy link to clipboard |
 Print this post |
|
Hi Bob thanks for the input i have done some research on the gear set's looks like there is around 6% loss per set then bearing loss, even if there is potential for loss up to 20-25% you can make up the extra power on the mast. I'm going to build the whole thing backwards from the ground up so when i have the generator running to my liking i can test rpm and torque these factors can be helped/increased with the use of gearing. the biggest downside i can see at the moment with the way i have it all set out is the torsional loss in the main shaft connecting the to right angle drives, I am hoping to use the ratio offset's to load the shaft and absorb the loss so to speak
Will keep you updated.
Aron If it ain't broke don't fix it |
|
VK4AYQ Guru
 Joined: 02/12/2009 Location: AustraliaPosts: 2539 |
Posted: 10:55pm 19 Sep 2010 |
Copy link to clipboard |
 Print this post |
|
Hi Aorn318
If it is HAWT you are doing one effect you will have is the torque reaction in the drive shaft turning the head out of the wind, that didn't happen with a VAWT, but may be an issue with a HAWT.
Will be interested in the progress.
All the best
Bob Foolin Around |
|
windlight Guru
 Joined: 03/03/2007 Location: AustraliaPosts: 331 |
Posted: 11:20pm 19 Sep 2010 |
Copy link to clipboard |
 Print this post |
|
I have never tried what you propose but Bob has a very good point about the torque reaction from the vertical shaft if it is a HAWT, but I would not place too much concern on losses, properly designed and allowed for.
With a HAWT it may be necessary to go to no tail and motor it into the wind, if the blade diameter is big enough that makes sense to me.
Looking forward to updates.
Allan "I like this place and willingly could waste my time in it" - (Act II, Scene IV). |
|
MacGyver
 Guru
 Joined: 12/05/2009 Location: United StatesPosts: 1329 |
Posted: 11:57pm 19 Sep 2010 |
Copy link to clipboard |
 Print this post |
|
aorn318
Whereas Allan has never tried what you propose, in 1973 I did. I used the bottom half of an outboard motor as the 90* direction changer and it just sat atop the tower and mocked me!
When there was enough wind to turn the thing, it'd move a little and no matter how big a tail I put on the thing, it would rotate the whole shebang out of the wind. Then the tail would move it back around into the wind flow again and it'd repeat its performance. I don't think it ever even spun one full revolution, because the gears just walked it around the vertical axis.
It was a great idea, I thought, but so was the Edsel. For those who don't know what an Edsel is, just imagine a mid-50s American sedan with a toilet seat hung upside down on its radiator; not much different.
. . . . . Mac
Nothing difficult is ever easy!
Perhaps better stated in the words of Morgan Freeman,
"Where there is no struggle, there is no progress!"
Copeville, Texas |
|
aorn318
 Newbie
 Joined: 05/09/2010 Location: AustraliaPosts: 20 |
Posted: 11:02am 20 Sep 2010 |
Copy link to clipboard |
 Print this post |
|
Thanks for the reply's
Mac just a quick question did the outboard drive system have spiral or bevel cut constant mesh gears if not you would have noticed a lot of gear resistance as the reversed force was applied to the now output shaft most outboards run an outer ring gear and a flat pinion when the drive force is reversed it forces the ring gear to offset on the pinion.
On the other hand yes gear walking could be an issue i'm hoping with a large amount of genius from a few electronics forum's to build a weather station well modify one to use the output data to run a stepper motor to keep the mill in the wind and also to automatically furl the mill and apply a shaft mounded disk break.
All a little more than the average back yard needs. but it will sure be fun ironing out the bumps along the way.
Aron If it ain't broke don't fix it |
|
VK4AYQ Guru
 Joined: 02/12/2009 Location: AustraliaPosts: 2539 |
Posted: 11:20am 20 Sep 2010 |
Copy link to clipboard |
 Print this post |
|
Hi Aron
Sound like you have a handle on the problem OK I look forward to seeing it develop and am sure that we can all offer suggestions to confuse you.
All the best
Bob Foolin Around |
|
aorn318
 Newbie
 Joined: 05/09/2010 Location: AustraliaPosts: 20 |
Posted: 11:26am 20 Sep 2010 |
Copy link to clipboard |
 Print this post |
|
Thanks Bob
confusion is the best way to find the answer the more i have to rethink any part of my design the better it will become
Aron If it ain't broke don't fix it |
|
VK4AYQ Guru
 Joined: 02/12/2009 Location: AustraliaPosts: 2539 |
Posted: 11:33am 20 Sep 2010 |
Copy link to clipboard |
 Print this post |
|
That's organized confusion. Also called fuzzy logic as compared to normal logic.
Bob Foolin Around |
|
aorn318
 Newbie
 Joined: 05/09/2010 Location: AustraliaPosts: 20 |
Posted: 11:39am 20 Sep 2010 |
Copy link to clipboard |
 Print this post |
|
I have a few ideas using basic robotics (following arm sort of thing) just need to nut out the sensors and there output data to use it to drive a stepper motor (sourced from an industrial automatic embroidery machine) any ideas?? If it ain't broke don't fix it |
|
aorn318
 Newbie
 Joined: 05/09/2010 Location: AustraliaPosts: 20 |
Posted: 12:55pm 20 Sep 2010 |
Copy link to clipboard |
 Print this post |
|
I though fuzzy logic was a washing machine with sh*tty motors for generator's although could be fun to pull one down and see where it goes but that can be latter.
I think i'm already chewing a big bite If it ain't broke don't fix it |
|
Downwind
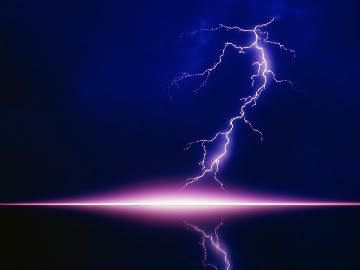 Guru
 Joined: 09/09/2009 Location: AustraliaPosts: 2333 |
Posted: 04:15pm 20 Sep 2010 |
Copy link to clipboard |
 Print this post |
|
There has been several discussions over time on electronic yawing and it has always been a big risk to trust the last line of defence to a sh*tty little microcontroller.
I hope that stepper is a powerfull sucker as you will need it, and how will you hold the yaw position, with electrical braking of the stepper motor? This will use some current to do this.
I am wondering if you can actually use gear walking to your advantage for furling.
I wish you luck with your project but think you have a can of worms to sort out.
Pete. Sometimes it just works |
|
rogeriko Newbie
 Joined: 10/08/2010 Location: GreecePosts: 4 |
Posted: 10:34pm 20 Sep 2010 |
Copy link to clipboard |
 Print this post |
|
Has to be the craziest idea ive ever heard of do you know how much noise all those bearings and spinning parts will make amplified 100s of times by a tower. Also you will need a motor to bring it up to speed because a stationary turbine blade has no power at all even in a gale so it will never be able to overcome bearing resistance etc on its own. Wacky idea maybe sell it to hollywood for a mad max movie. |
|
aorn318
 Newbie
 Joined: 05/09/2010 Location: AustraliaPosts: 20 |
Posted: 02:08am 21 Sep 2010 |
Copy link to clipboard |
 Print this post |
|
thanks roger love your work but bearing and gear resistance is only the same as cogging in a big generator so we will see how i go and if all else fails i can sell the design If it ain't broke don't fix it |
|
aorn318
 Newbie
 Joined: 05/09/2010 Location: AustraliaPosts: 20 |
Posted: 11:39am 23 Sep 2010 |
Copy link to clipboard |
 Print this post |
|
hi pete
have been playing around with the stepper motor plan and well bluntly it would need to be the size of a small car to hold the weight so that's out
but im not giving up yet just made the design simpler a little more engineering but less to go wrong take out all electronics and go back to simple physics
if the blades turn left or anti-clockwise then its safe to say the main shaft will turn right or clockwise through one gear set this would make the mill try to turn to the left with gear walk with a large tail at an offset angle to the right yet to be determined forcing the mill to turn against the gear walk then a simple sprag clutch set to stop the mill turning with the gear walk the only down side is that if the wind throws back where it came from the mill will die out but that's another problem for later
might be able to use a double offset sprag with a control arm acting of wind direction to pull one sprag in and the other out allowing the mill to turn with the gear walk
will keep up ideas and pics when i have them
Aron If it ain't broke don't fix it |
|
VK4AYQ Guru
 Joined: 02/12/2009 Location: AustraliaPosts: 2539 |
Posted: 12:54pm 23 Sep 2010 |
Copy link to clipboard |
 Print this post |
|
Hi Aron
I think the only to to neutralism the torque reaction is to use a complicated dual drive system with counter rotating shafts set up coaxually as in a counter rotating propeller drive on an aircraft.
All the best
Bob Foolin Around |
|
Trev
 Guru
 Joined: 15/07/2006 Location: AustraliaPosts: 640 |
Posted: 05:46am 25 Sep 2010 |
Copy link to clipboard |
 Print this post |
|
aorn318,
I have been down the road with gearing. I have posted somewhere here before. I just tried to search but don't find where I posted so here I have copied the links from my memberlist. You will need to go to my memberlist file to be able to view the pictures.
2008-01-02_215936_2a.JPG
2008-01-02_220043_2b.JPG
2008-01-02_220132_2c.JPG
2008-01-02_220222_6.JPG
2008-01-02_220348_7.JPG
2008-01-02_220448_8.JPG
I have tried belt drive combinations and car diff drive.
The right angle diff drive does have the gear walk issue. I used a very large tail and 6 F/glass composite blades that normally make up my 2.9m diameter blade set, but with the bigger 6 blade hub was about 3.1m diameter. This machine did work, but never produced any more power (watts) than the single F&P motor direct drive with 2.1m diameter f/glass composite blades.
To make a geared machine work you need a very large prop diameter to overcome all the losses. No real benefit for all the extra work, extra weight and stronger tower required and the extra cost to set it up.
I hate to spoil your fun though. Go ahead and let us know what you discover.
Trev @ drivebynature.com |
|
|
Page 1 of 2 |