Author |
Message |
Mickus Newbie
 Joined: 14/11/2011 Location: AustraliaPosts: 17 |
Posted: 04:46am 03 Oct 2013 |
Copy link to clipboard |
 Print this post |
|
What parts do people use to connect to a shaft like this.
|
|
brucedownunder2 Guru
 Joined: 14/09/2005 Location: AustraliaPosts: 1548 |
Posted: 10:20am 03 Oct 2013 |
Copy link to clipboard |
 Print this post |
|
Hi there,
It's such a little shaft ,I'd use a brass electrical wire connector . Take the plastic shroud off it and you'll find the earth type ones have two "grub" screws that should secure well, if you are worried , a dob of super glue or "Locktite" on the grub screw threads will stop it from becoming loose.
3 mm is a little over a bicycle spoke ,so it's very small and should not have too much mechanical stress on it ?
Bruce. Bushboy |
|
Mickus Newbie
 Joined: 14/11/2011 Location: AustraliaPosts: 17 |
Posted: 12:47pm 03 Oct 2013 |
Copy link to clipboard |
 Print this post |
|
Thanks, I will head into Jaycar. Would the cut out side and grub screws going into it cause the shaft and hub to be unbalanced?
Or as it is so small, it cant produce enough stress. |
|
M Del Senior Member
 Joined: 09/04/2012 Location: AustraliaPosts: 155 |
Posted: 09:26pm 03 Oct 2013 |
Copy link to clipboard |
 Print this post |
|
Hi
It may be slightly unbalanced but any problem would depend on the length of the shaft and the speed at which it is rotated.
I have used similar in items built years ago, meccano for the kids and scale model demo gear for winches and cranes and used one (6mm) recently to modify a car heater fan motor connection.
The connectors also make a dandy bbq gas control knob when the original knob brakes, a lot easier than a pair of pliers.
Mark
Mark |
|
Mickus Newbie
 Joined: 14/11/2011 Location: AustraliaPosts: 17 |
Posted: 04:16am 04 Oct 2013 |
Copy link to clipboard |
 Print this post |
|
Seeing as the connector is brass, I could try to solder on a small counter weight. But I bet I will continually chase the balance and end up with a 1kg connector.
|
|
M Del Senior Member
 Joined: 09/04/2012 Location: AustraliaPosts: 155 |
Posted: 03:06pm 04 Oct 2013 |
Copy link to clipboard |
 Print this post |
|
Unless you are fitting it to the end of a 12 inch shaft or spinning it at high revs there should not be a problem.
What are you using for?
Mark |
|
Bryan1
 Guru
 Joined: 22/02/2006 Location: AustraliaPosts: 1344 |
Posted: 04:12pm 04 Oct 2013 |
Copy link to clipboard |
 Print this post |
|
What I've done in the past with a flat on a shaft is cut down a shaft the same internal diameter to form a 1/2 round key then once assembled drill 2 holes then pin the key. This way the connector is in full balance and I haven't had one brake on me yet.
Cheers Bryan |
|
Downwind
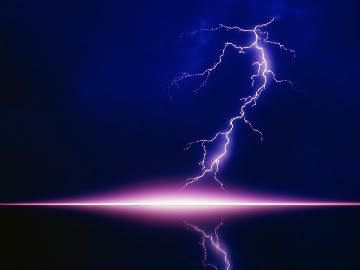 Guru
 Joined: 09/09/2009 Location: AustraliaPosts: 2333 |
Posted: 06:19pm 04 Oct 2013 |
Copy link to clipboard |
 Print this post |
|
A section of tube off a car antenna to fit snuggly and a dob of super glue into the D. (and i dont mean for you to go shopping in the pub car park for an antenna)
Or look into remote control cars, the electric ones use motors with 3mm shafts by memory, and high torque motors, as some do close to 100kph.
Pete. Sometimes it just works |
|
Mickus Newbie
 Joined: 14/11/2011 Location: AustraliaPosts: 17 |
Posted: 11:11pm 04 Oct 2013 |
Copy link to clipboard |
 Print this post |
|
It's a small wind mill to run a single LED light, trying to get the kids interested
I am also using similar small motor to fan a heat sink on a peltier generator im
Playing around with. Both builds are very small scale due to limited tooling
Machines and no backyard mechanics nearby in Brissy that I can befriend haha |
|