Author |
Message |
Highlander
 Senior Member
 Joined: 03/10/2006 Location: AustraliaPosts: 266 |
Posted: 07:47am 19 Dec 2006 |
Copy link to clipboard |
 Print this post |
|
G'day guys I've been trying to come up with a way to make twisted blades that doesn't require too much carving. I found it nearly impossible to get a piece of wood big enough to carve a decent blade that didn't have knots all through it. So I had this idea from my previous boat building work. Unlike building a boat this wood is unsupported so it just a try and see how it goes sort of thing.
I started with 19mm marine ply 1200mm by 600mm and cut an elongated coffin shape out with the middle one up side down to maximize use of the wood.
I then left them to soak in a wheelie bin full of water for three weeks. I made a jig on a bench to clamp them to, clamped them in and left to dry, so far about 4 weeks drying.
Now comes to the bit I'm not sure of, I think I'll carve the aerofoil shape on them and poly resin them to seal from the wheather, I think resin would be better than paint as it should soak into the wood a bit and possibly help them hold their shape. It's also a bit more durable I think.
Any suggestions ?
PS if your wondering why I twisted it like that it's to fit the alum prop hub made by Trev
BTW the wood cost $30Edited by Highlander 2006-12-20 Central Victorian highlands |
|
Gill
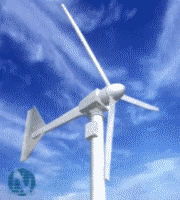 Senior Member
 Joined: 11/11/2006 Location: AustraliaPosts: 669 |
Posted: 11:22am 19 Dec 2006 |
Copy link to clipboard |
 Print this post |
|
Great idea, though you already suspect the potential week spot I see, being not holding shape over time. With boat building isn't this twisted panneling secured to a frame and or other hull structures to maintain it's shape? Unsupported, any return to it's origonal flatness would cause most trouble if they were to not untwist at the same rate. Still worth a try. Though I would suggest laminating several thinner sections where they were glued and clamped to the desired shape. I saw a yacht built where with the first layer of ply, the ply grains were say verticle and horizontal. The next layer was diagonal then back to verticle and horizontal for the 3rd layer. Not very economical use of ply sheets, yet thats how it was done and the curves involved were not gentle. With the setup you have now I think the resin idea is better than paint, but fiberglass the lot as painted on resin will crack with heat expansion then the water soaks in. I like the basic idea though. was working fine... til the smoke got out.
Cheers Gill _Cairns, FNQ |
|
Feral Newbie
 Joined: 03/12/2006 Location: AustraliaPosts: 39 |
Posted: 03:37pm 19 Dec 2006 |
Copy link to clipboard |
 Print this post |
|
The Polester resin will not like the timber especially if it has any moisture at all in it. Epoxy resin in a dynal cloth would be better and the dynal would help to hold the shane of the blades and give more strength.
In the event that your ply blades are not successful try shaping some polyurethane foam and fibre glassing with polester resin and place timber only at the area of blade where bolts fix to hub.
The foam is very easy to shape and very light but the strength come with the FG. |
|
Highlander
 Senior Member
 Joined: 03/10/2006 Location: AustraliaPosts: 266 |
Posted: 07:19pm 19 Dec 2006 |
Copy link to clipboard |
 Print this post |
|
Gill, thanks for that, but you must have missed the part where I wrote;
"Unlike building a boat this wood is unsupported so it's just a try and see how it goes sort of thing."
I did consider using multiple sheets laminated but it adds an incredible amount of time and wood, basically I was looking for a quick easy method. Only time will tell how they hold up.
I think after time they will revert back to a flatter shape, but with centrifugal forces they will probably do it at the same rate. If they don't they'll vibrate, break off and fly into the paddock (big deal), but considering for $30 plus coating, if they only last even 6 months then they're still good value. I probably wouldn't try this in the suburbs though
Central Victorian highlands |
|
thefinis Regular Member
 Joined: 23/08/2006 Location: United StatesPosts: 53 |
Posted: 01:35pm 20 Dec 2006 |
Copy link to clipboard |
 Print this post |
|
If they can be waterproofed so no moisture gets in it should work. I expect that they may flatten out a little when first removed from the clamps. After they stablize and then are waterproofed they should be fine. Moisture will cause it to remember its old shape if not supported. Resin and a binder(fiberglass or other) will act as a limited support and waterproofer. I did not have trouble with fiberglass patching on dry wood but usually roughed it up a little with sandpaper.
Feral I thought that the poly resin would eat the foam. With foam you normally use epoxy and binder cloth.
Finis Texas born and bred |
|
Highlander
 Senior Member
 Joined: 03/10/2006 Location: AustraliaPosts: 266 |
Posted: 03:41am 21 Dec 2006 |
Copy link to clipboard |
 Print this post |
|
Hey Finis, no flies on you mate.
(that's an aussie term meaning your smart)
The marine ply will flex back a bit after being declamped, I added another 8 degrees of twist to allow for this.
I went to a fibreglass manufacturers trade outlet today and he said "mate I'de love to sell you something but the best product for this application is moisture cure urethane, which you can get at a flooring/paint shop."
Apparently this stuff soaks right into the wood adding strength and completely seals the surface. Perfect.
Central Victorian highlands |
|
Highlander
 Senior Member
 Joined: 03/10/2006 Location: AustraliaPosts: 266 |
Posted: 06:05am 21 Dec 2006 |
Copy link to clipboard |
 Print this post |
|
G'day guys, I got some of the moisture cure stuff, three times the price of the blades $91 for 4 litres and 500ml of thinner.
But still the total is pretty good for twisted blades.
If anyone else tries this I cannot stress enough that you need to soak marine ply for WEEKS about three is good. If your in a high humidity area you may need to build a box surrounding the area and insert a heat source when your drying them. Central Victorian highlands |
|
Trev
 Guru
 Joined: 15/07/2006 Location: AustraliaPosts: 640 |
Posted: 12:46pm 21 Dec 2006 |
Copy link to clipboard |
 Print this post |
|
Excellent Highlander, good to see you have a go.
I would have thought if you have experience with boat building (timber) and F/g then did you not know that epoxy resin is the choice?? Thats what most timber boats are sealed with. But then I don't know everything, this moisture cure urethane, can you email me the label, any info you have on the stuff, I'm curious...
Polester resin does work in sealing the timber too, but not as strong. I have used it numerous times. Moist timber would be the same as high humidity. Above 75% humidity is not workable with F/g.
I'm interested to see if they hold there shape?? Glass fibre would assist in holding the shape.
Polyurethane foam does not melt with polyester resin or epoxy resin. Polystyrene foam will melt with polester resin but not with epoxy resin.
Keep try'n Trev @ drivebynature.com |
|
Highlander
 Senior Member
 Joined: 03/10/2006 Location: AustraliaPosts: 266 |
Posted: 01:36pm 21 Dec 2006 |
Copy link to clipboard |
 Print this post |
|
G'day Trev, I'm not a tradie boat builder I've just made a few they were all wood with grp coat. So yes your right but I wanted to avoid the messy fg work so that's why I was looking at something like this that will soak in and seal. The wood has enough strength of it's own, it just needs to be sealed. But then again I'm not always right either, most of my learning is the result of trial and error, (with lots of errors)
Edited by Highlander 2006-12-22 Central Victorian highlands |
|
Feral Newbie
 Joined: 03/12/2006 Location: AustraliaPosts: 39 |
Posted: 05:02pm 21 Dec 2006 |
Copy link to clipboard |
 Print this post |
|
Thefinis, Its more complicated than that, some years ago we had access to two types of polyester resin and either could be used on polyeurthane foam from memory but only one of these could be used on closed cell PVC foam. I learnt the hard way and that is why I would be reluctant to put polyester resin on the timber blades that had been immersed in water for three weeks. In the past I have spent a lot of time replacing ply timber transoms in the rear of FG boats and any moisture in the new ply sheets used in the transoms caused ploblems with the FG sticking to the ply. The epoxy resin is a better choice for gluing to the timber but with the dynal (synthetic fibre) it is what was in common use for laminating over, boats constructed with ply, as a protective skin. Polystyriene foam is another one thats requires the use of epoxy. |
|
Highlander
 Senior Member
 Joined: 03/10/2006 Location: AustraliaPosts: 266 |
Posted: 09:34pm 21 Dec 2006 |
Copy link to clipboard |
 Print this post |
|
Hey Feral I understand your concerns, but they have been drying for 4 weeks so far, and I was planning on another week more with the heater in the box surrounding it. So they should be bloody dry after that. In the event that there is still moisture there, the moisture cure polyurethane should work just fine. Here's a close up of the can.
This will also cure from moisture in the air and doesn't use glass or other reinforcement as it's a coating.
Trev I noticed a FGI can in one of your pics, they're the guys that advised me to use what I bought.
FGI being a manufacturer with their team of chemists and R&D facility would have been the best ones to consult, I thought. I went to the Melb plant (not a reseller) and a few guys were involved in the discussion and that was what they all agreed on. So if they're wrong, God help me, and I'll try something else. Central Victorian highlands |
|
thefinis Regular Member
 Joined: 23/08/2006 Location: United StatesPosts: 53 |
Posted: 06:22am 22 Dec 2006 |
Copy link to clipboard |
 Print this post |
|
Feral it was my bad on the foam I knew better from reading other posts. I have played with foam but never put resin on it.(yet) The foam as I use it needs uv protection more than support. Read that even with the foams that are fine with poly resin that you need to be careful during curing. It can get too hot and the foam will shrink or warp.
Out in west Texas I have used fg to patch small areas on canoes and sailboats but usually only after they had been stored over the winter. Never really worried about the patches sticking to any wood and if it needed to attach to a rib just added ss screws and glassed over the heads. At the time I had not heard of using epoxy for glassing except for emergency patches.
I have some wings that use ply that I am going to need to seal. Highlander needs his blades to keep a twist while I need my pieces to stay flat. I understand the concern that the wood be dry as a coating will trap any moisture in as it keeps moisture out. Highlander I hope that your moisture cure polyurethane is UV resistant. Out here I would have to spray water on it to get enough moisture to cure. I have been looking at polyurethane spar varnish or deck coatings.
Finis
Texas born and bred |
|
Feral Newbie
 Joined: 03/12/2006 Location: AustraliaPosts: 39 |
Posted: 04:42pm 22 Dec 2006 |
Copy link to clipboard |
 Print this post |
|
Thefinis, I am not sure where Highlander is located but where I have been residing in the past twelve months we had six Mts (20 Ft)of rain and there is no lack of moisture.
As for the ply would like to keep plat I would suggest that if you have no moisture problems you look at vacumbagging the sections of ply or timber and have a epoxy resin induced after the vacume is reached. It is a very simple process and one that ensures that the resin is drawn into the paws of the timber for a better seal of the surface. Ask around at any boat building factory and they would be able to explain the process. It can be done with a normal compressor and a range of fittings and valves to allow the thin epoxy resin or twopack epoxy paint to be drawn into the timber without allowing air back into the sealed bag around the flat timber you are trying to seal and stabilise. I also learnt this procedure the hard way and did not cause to much double work in the process. The epoxy does not need exposure to the atmosphere as the chemical reaction dries and hardens the epoxy.
When using polyester resin on closed cell PCV foam there is only one resin that is suitable and one thing that should be done as per the manufactures instructions is the persentage of catylist or hardner as it is this that causes the heat if the percentage of hardner is to high and causes to much heat in the curing process. |
|
Highlander
 Senior Member
 Joined: 03/10/2006 Location: AustraliaPosts: 266 |
Posted: 07:24am 04 Jan 2007 |
Copy link to clipboard |
 Print this post |
|
Well the blades turned out well.
They did lose a bit of their twist after the carving of the aerofoil shape was done. The wood which was removed must have been holding some of the twist. It would be better to cut the shape out, carve and then soak and twist. But if you do this you can't stack the blades on top of each other when clamping, due to the wing shape on the blades. So three separate jigs will need to be made for them to dry out in.
I did find a better coating, it's called "spar marine" made for high uv and tough marine conditions.
Yes this is totally experimental. If they hold up well then it's a bonus. Central Victorian highlands |
|