Revlac
 Guru
 Joined: 31/12/2016 Location: AustraliaPosts: 1022 |
Posted: 10:11am 27 Jul 2022 |
Copy link to clipboard |
 Print this post |
|
We have an old air VA100 air compressor and its the second time the oil sight glass has cracked and leaks oil, its not that cheap to keep replacing this, so how hard is it to make one?
Drawn up the outline in Inkscape then opened it in jscut to edit and convert it to Gcode, to be Cut with the little 3018 Pro CNC mill. I had some spare 20mm perspex to use, ideal for this job, the settings are as follows.
Standard 4 flute cutter that come with the cnc Pass depth .2mm Step over .25 ( 1/4 the size of the bit) Plunge 127mm/min Cut 500mm/min
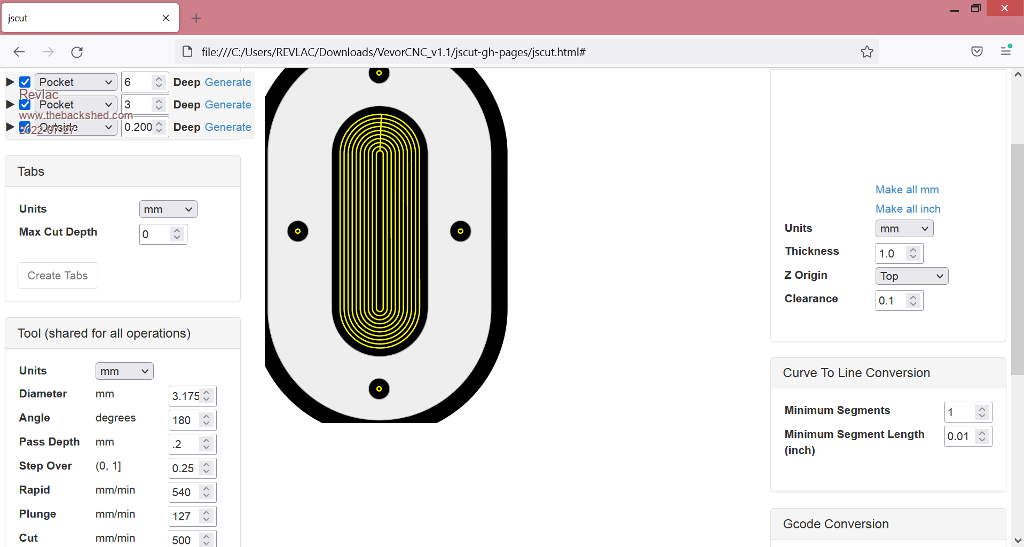 The spindle speed was about half speed, 4000rpm or 5000rpm, unfortunately Candle had locked the speed setting and cant change it yet, I know the spindle will go a lot faster (twice as fast) with the offline controller. Started cutting very well, it did chatter and vibrate a little but did not effect quality of the job.
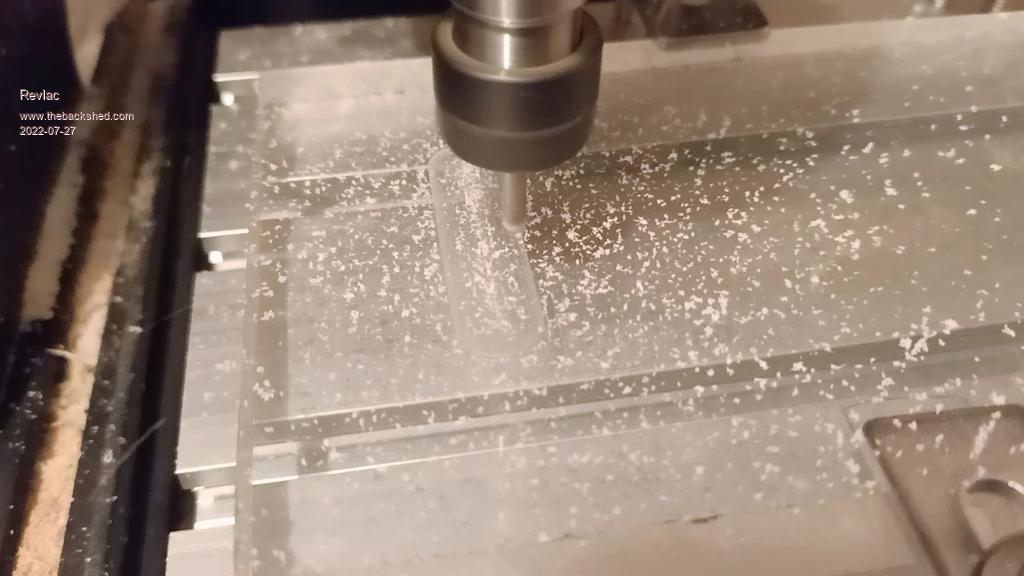 The center cut out went great, but cutting those small holes heated up the mill cutter, should have had air cooling for those, after cutting those 4 holes it then started cutting the perimeter, you can see the cutter was still too hot and produced feathering (white fluffy cut) but after the cutter cooled off a little it was cutting clean again. Edit: Total cnc running time for this job was 26 minuets.
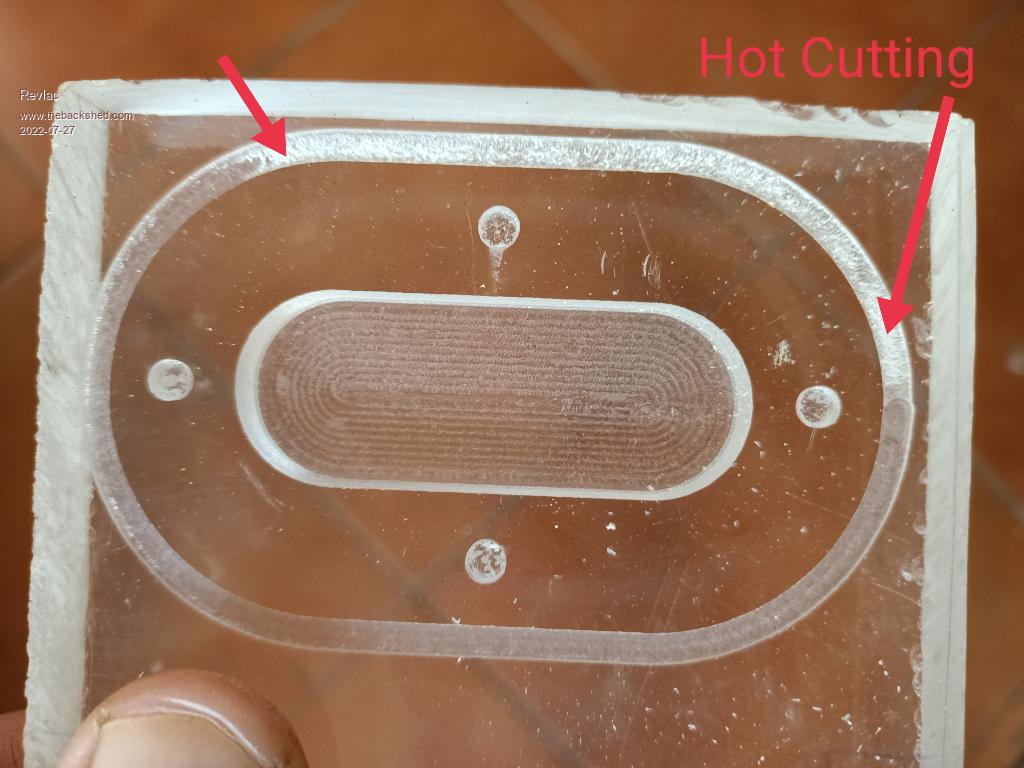 Next task was to line it up in the K40 Laser cutter ( max cut I read about was 4mm?) this is 20mm perspex, after practising with an off cut, I found that it will cut that thickness (not neatly) if the focus point it halfway though the perspex, so 8mm to 10mm deep, would not do that with wood it would just burn it wide. Set the power to 40% and 3mm per second travel, it cut 6mm deep on the first pass and more on the second pass the 3rd pass was almost through but upon checking it, I bumped the perspex and knocked it out of alignment.... Fixed it up and did another 2 passes, so 5 passes all up, would have done it in 4 I think. It caught fire twice on the first cut, there was a little bit of fluff in the way of the laser, should have had forced air on the job to blow out the fire the rest of the cutting was trouble free.
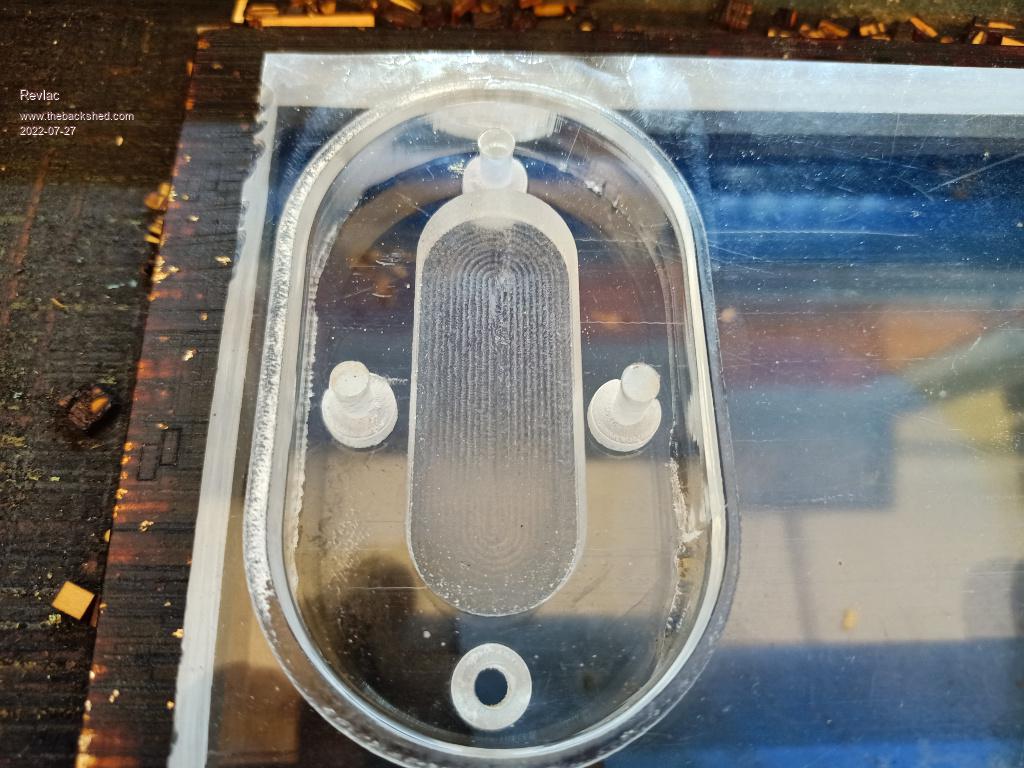 End result.
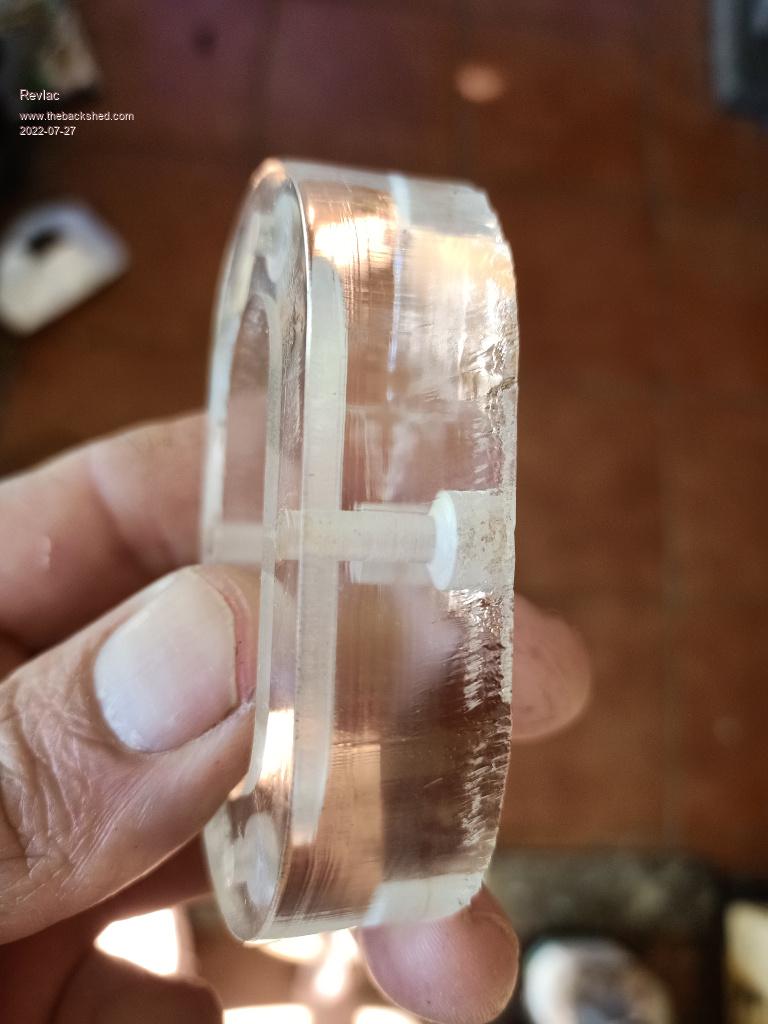 Like a hot knife through butter
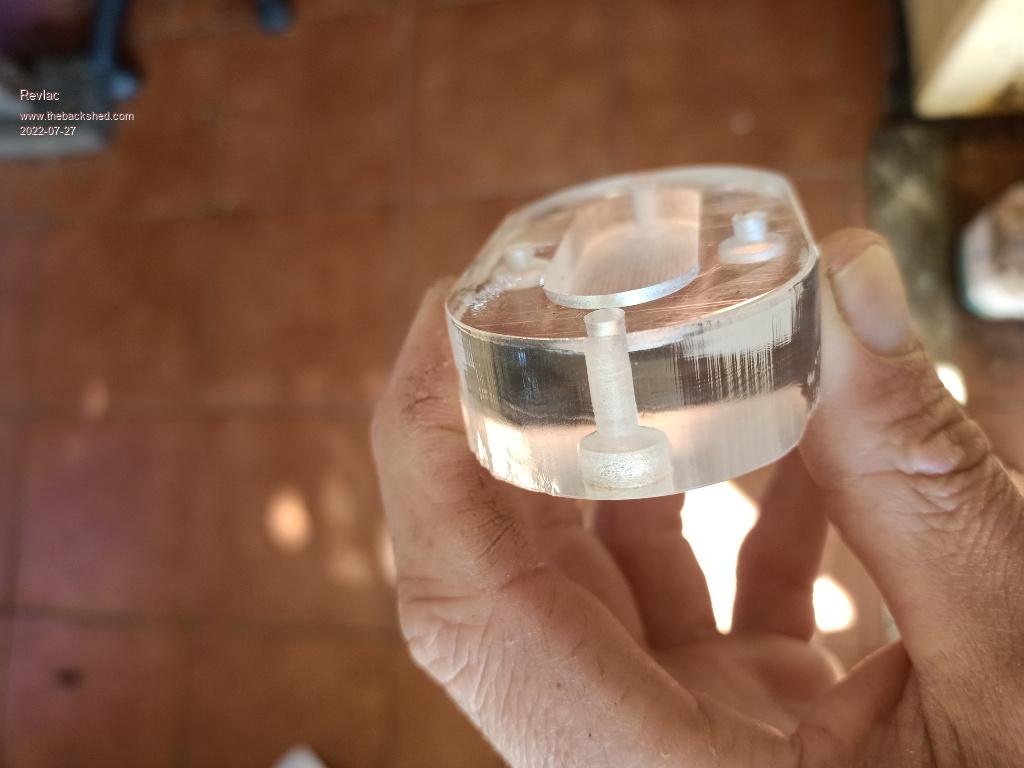 Overall the 3018 pro with the Bakelite side plates is fairly sturdy, but still a bit of let down with those 10mm rods that flex a little, however that did not effect the project, probably added to the vibration, the standard motor did not even notice any load cutting this stuff. Would like to try the single flute cutter later and get the spindle speed up a bit more. Anyway Just thought the settings might be helpful for someone starting out.... Edited 2022-07-27 23:04 by Revlac Cheers Aaron Off The Grid |