Author |
Message |
SSW_squall
 Senior Member
 Joined: 20/03/2010 Location: AustraliaPosts: 111 |
Posted: 05:18am 25 Mar 2010 |
Copy link to clipboard |
 Print this post |
|
Following on from the price watch post about the Oatley electronics MPPT unit.
Incidentally, for a while Oatley were posting the full kit instruction manuals online, including the schematic, however situation didn't continue for long.
Altronics now have a range of MPPT controllers with specs that rival the OUTBACK FLEX MAX ect.
http://www.altronics.com.au/index.asp?area=item&id=N2032
Sold by an Australian company GSL based in Sydney:
http://www.gsl.com.au/index.html
The prices are quite reasonable too:
Retail: $385
Wholesale: $250
The display module is extra:
Retail: $252
Wholesale: $134
I'm sizing one up for my 48V micro hydro rig...
Einstein: Everything should be made as simple as possible, but not one bit simpler |
|
GWatPE
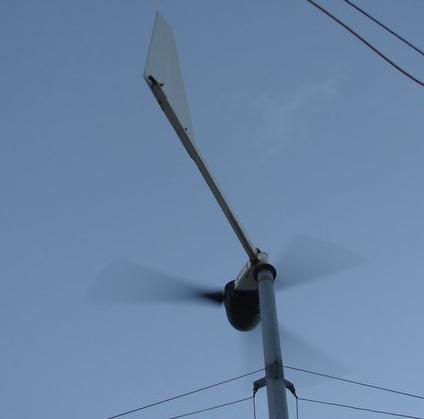 Senior Member
 Joined: 01/09/2006 Location: AustraliaPosts: 2127 |
Posted: 11:07pm 26 Mar 2010 |
Copy link to clipboard |
 Print this post |
|
The unit may be suitable for modification to convert to a buck type windmill MPPT. The 1500W rating, and up to 95V input are useful.
The unit does have a sizeable heatsink, and looks like fan ventilation slots, 97% efficiency amounts to 45W loss at full power, so a fan would be needed, even with the large heatsink.
I am surprised that low efficiency units are still being made, considering units above 99% efficiency were commercially available.
At $385, the units would be quite good value for solar as is, and even modding for a windmill.
Gordon.
become more energy aware |
|
SSW_squall
 Senior Member
 Joined: 20/03/2010 Location: AustraliaPosts: 111 |
Posted: 12:15am 27 Mar 2010 |
Copy link to clipboard |
 Print this post |
|
Fairly sure the unit would already be a "buck" or step down style convereter - Input voltage range is 15-95V.
All the MPPT controller i've seen at operate in this way for a couple of reasons:
1. It's alot easier to make a "buck" style converter with high efficiency than a "boost" converter, less switching losses with higher input voltages.
2. Higher input voltages mean less cable losses from panels to the MPPT controller.
3. Engineers designing such units conform to the adage - "Give the hardest job, to the laziest man and he'll find the easiest way"
The outback MPPT manuals advise that it better to have a some extra solar panels to deliver extra voltage over the top of the battery bank.
Because in some conditions (high temperature) the MPPT can't actually step down the voltage to work properly.
So all it does in these circumstances is connect the panels directly to the batteries...
Einstein: Everything should be made as simple as possible, but not one bit simpler |
|
GWatPE
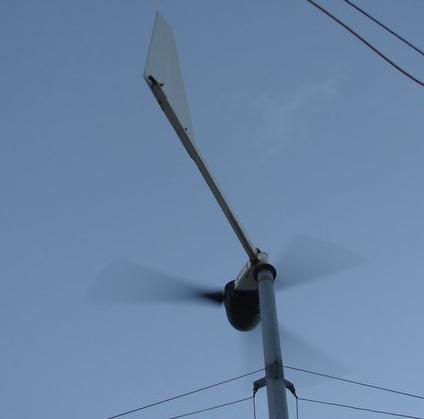 Senior Member
 Joined: 01/09/2006 Location: AustraliaPosts: 2127 |
Posted: 02:09am 27 Mar 2010 |
Copy link to clipboard |
 Print this post |
|
The unit will be a buck type solar panel MPPT only. The unit may be suitable to convert to a buck type "Windmill" MPPT. This is a little better wording.
Windmills have completely different power output characteristics to solar panels. Solar panels are basically a constant voltage, variable current power source, while a windmill is a varying voltage, varying current power source.
The high efficiency modern GTI use a boost style input, not a buck. DC OFF Grid systems tend to be low voltage/high current, so any system that reduces conductor sizing is appropriate.
You have stated that it is easier to make a high efficiency buck converter. This view may not be shared by some forum members who have tried.
The switching losses can be low in any well designed buck or boost converter.
For a windmill, the boost converter type can be 1/5 the power handling capacity of a buck, for the same power windmill.
The power electronics of the buck unit present the most difficulty for DIY. The internal converter high current/high voltage switching transients present the most problems for DIY builders.
I had spoken to AERL designers, and have one of their 99.7% efficient coolMAX buck units. The lengths that they went to are extraordinary, and even at 1kW power transfer, the unit operates at around 40C, and there are no heatsinks or fans. I am not sure if the company still operates, so another alternative commercially available unit would be a good start for a "Windmill" Buck MPPT, without having to make all from scratch.
Gordon.
become more energy aware |
|
SSW_squall
 Senior Member
 Joined: 20/03/2010 Location: AustraliaPosts: 111 |
Posted: 03:38am 27 Mar 2010 |
Copy link to clipboard |
 Print this post |
|
Good comments, Gordon
I didn't say it would be (that) easy...
It isn't too hard to come up with a design that works OK, but one that works efficiently, has protection features and does not use overly esoteric or expensive components is not so easy.
The subwoofer amp electonics i've been designing at work for the last 6 months illustrates the point:
The make signal processor only uses 4 TL072 OPAMP's and 6 digital potentiometers IC's controlled by a PIC; What could be easier??
Getting the noise and hum down below 10mV at the loudspeaker when connected to a 400W amplfier module driving a sensitive 90dB/2.83vrms/1m loudspeaker with an overall voltage gain of almost 50dB has been absolutely NON-TRIVAL!!
End off-topic
It makes sense that GT inverter's would use a boost converter.
My guess would be a half-bridge transformer isolated forward converter that generates a +340v rail. This would then be PWM switched by a H-bridge across the AC line to export the power to the grid.
When i was at Uni i designed and built a forward converter that could deliver 250W from 12V, based around the TL494 IC and 2 pairs of IRFZ44 MOSFET's.
Also made a small one to power a vaccum tube DI box, but i could get rid of the switching noise to a sufficent degree through. The DI box did work great when i changed to a linear regulated supply.
If i was going to design a high power MPPT buck converter i would definitley go for a multi phase synchronous topology: great efficiency, less output ripple, smaller output filter components ect ect
You'd also want to go for N-ch MOSFET devices for lower loss, so that implies high side drive which is extra complication.
International rectifier have some excellent solutions for multi-phase converters, that do the heavy lifting in terms of making sure the average current from all phases is zero.
Add in protection feature and a microcontroller is a neccesity.
This kind of thing is definitely out of the realms of the average DIYer.
One of the main things limiting the roll out of more RE setups is the access to cost effective power electronics.
Only in the last few years have reliable high power inverters become avaliable at anything approaching reasonable prices.
Everything to do with better innovation, engineering and design.
POT SHOT: Maybe some of these extremist greenies should do engineering and start contributing to the solution, rather than whining about the problem!!
Off-topic again!!
Getting back to the wind turbine MPPT:
You'd probably want a voltage clamp to limit the input voltage to below the max 95v spec.
And maybe some sort of minimium power connect circuit to ensure that the turbine doesn't stall before it has a chance to spool up properly.
But what else would (or could) you change to help the MPPT unit follow the cubic power law curve of the turbine??
AB
Einstein: Everything should be made as simple as possible, but not one bit simpler |
|
KarlJ
 Guru
 Joined: 19/05/2008 Location: AustraliaPosts: 1178 |
Posted: 05:18am 27 Mar 2010 |
Copy link to clipboard |
 Print this post |
|
I think Gordon did this for a long time (windmill MPPT) and is doing it again now, but for simplicity Gordons CAP voltage doubler is hands down winner -even if you do miss out on a few watts here and there over a vastly more expensive and complicated MPPT idea.
Luck favours the well prepared |
|